Uudised
The role of the 5S system in providing logistics services
Did you know that the 5S system can help reduce waste and save company costs? With an organized and standardized workspace, employees can easily find what they need, reducing time spent searching and increasing time spent on value-adding tasks. The 5S system also helps to reduce waste and streamline processes, and lead to cost savings and quality improvement. In this article, you can get an overview of what 5S is, how we at Logistika Pluss have implemented it, and what we have planned for the future.
5S is a system created by the Japanese for organizing rooms so that work can be done efficiently, correctly and safely. The system focuses on keeping everything in its designated place and keeping the workplace clean. The organization of things helps people make their work easier without losing time and reduces the risk of injury.
5S comes from five Japanese words:
SEIRI Sort
SEITON Straighten
SEISOU Shine
SEIKETSU Standardize
SHITSUKE Sustain
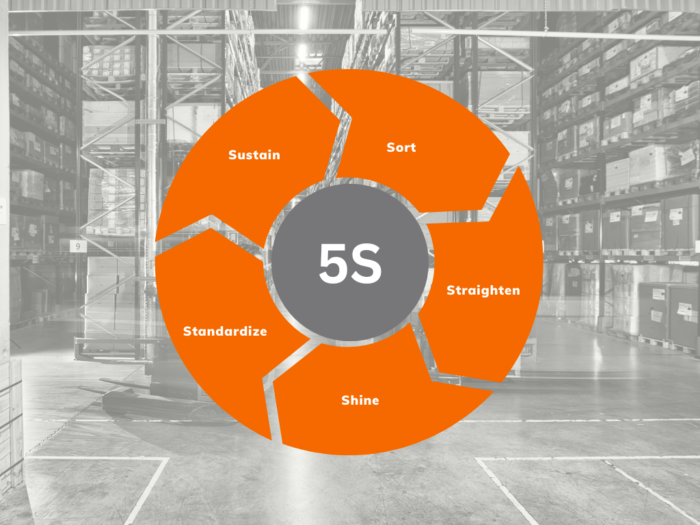
Each S represents one part of a five-step process that can help improve the overall functioning of a business:
1. Sort: The first step is to organize your work spaces by sorting and removing everything that is not necessary. This includes tools, equipment and materials that are unused, broken or out of date.
2. Straighten: Once the unnecessary items have been removed, the remaining items should be assigned a specific place so that everyone can find and return them immediately if necessary.
3. Shine: In order for the work environment to remain safe and function efficiently, work surfaces and floors must be regularly cleaned and equipment maintained.
4. Standardize: Procedures and processes should be standardized to ensure consistency and reduce variability. This can include everything from documentation to how to use the tool.
5. Sustain: The fifth step involves creating and maintaining a discipline where employees are engaged and motivated to follow the principles of 5S.
The 5S system has been in use at Logistika Pluss for many years. If previously we used the Excel methodology, from 2023 we have a special app, with which we conduct 5S audits and thanks to which we can now do it even more efficiently. Our logistics centers are divided into 7 different areas. There are areas where audits are conducted over a week and areas where once a month.
The process looks like this: the responsible person organizes the audit, it is carried out and the results are fixated. If irregularities are found, the results are reflected on our information TVs on the walls or on a white board in the units, so that all employees are informed and can carry out their activities accordingly in the future.
Then, in case of non-conformities, the employees responsible for the maintenance of the areas must implement corrective actions and solve the discovered problems and non-conformities.
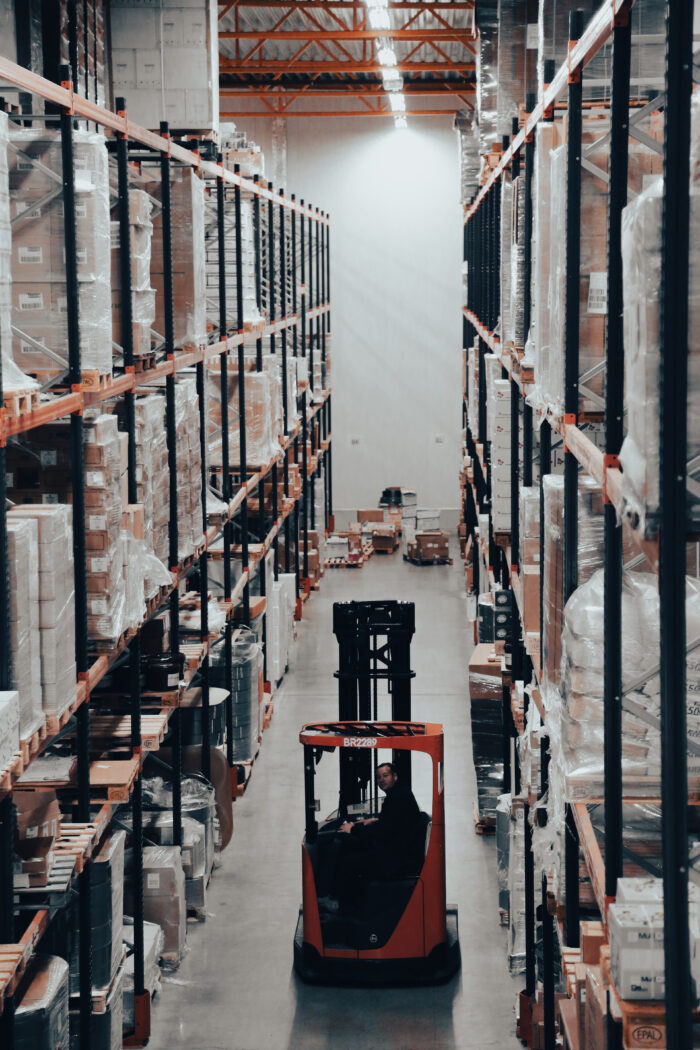
We also have a special 5S metric with a set goal, and we monitor it both at the level of departments and management, as we consider it very important that our logistics centers are clean, tidy and work efficiently.
We believe that the 5S system has affected the morale and job satisfaction of our employees. When there is order in the warehouse, it is easier for people to do their jobs. If the working tools are in their right places and marked, it allows to work more efficiently, save time and resources. If the work environment is safe, employees feel good and work is more pleasant. With the help of 5S, keeping order has become a habit for employees. New employees will also be trained about 5S immediately.
This year we have taken the first steps to improve our 5S system and create the ground for 6S. The additional “S” means Safety. During the safety step, the entire warehouse area is inspected and risks at workplaces that may cause injury to the employee are analyzed. Then standards are created for workplaces, which all employees must follow in a given workplace and which would be in line with safety requirements. Since April, we have supplemented our 5S with safety checkpoints related to working with forklifts.
Our company has fully adopted the Japanese 5S system and we apply it in all areas of our operations. In this way, we achieve higher efficiency and quality, reduce machine downtime, make better use of storage areas and ensure work safety. Our customers can be sure that the goods are well stored with us, and this is certainly partly thanks to the 5S system.
***
Over time, the 5S system brings many benefits, including:
• Reduced costs
• Higher quality
• Increased productivity
• Greater employee satisfaction
• A safer working environment